Myself and Kane have been giving Stew a hand sorting out some rot on the big yellow race bus, replaced a rotten corner on the wing, and currently working on the passenger sill, also waiting on an arch repair panel (ironically ordered by Stew when i started research on them the other night lol
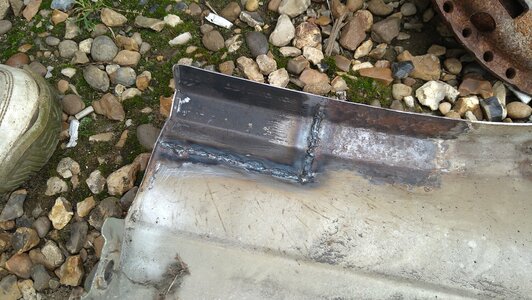
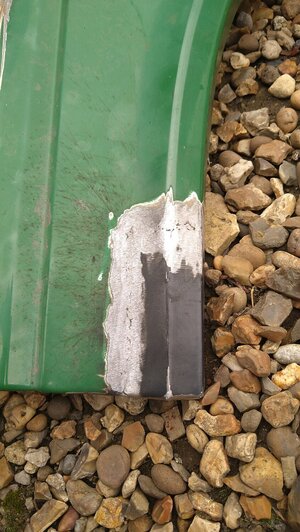
We did both rear suspension mounts and the exhaust, along with the left rear sill a couple of years ago, but this lot needs doing for mot so he can flog it
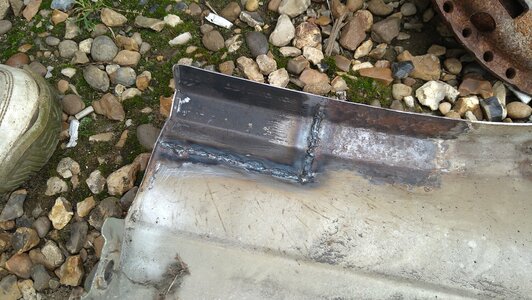
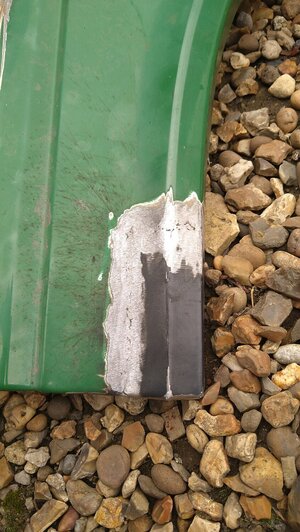
We did both rear suspension mounts and the exhaust, along with the left rear sill a couple of years ago, but this lot needs doing for mot so he can flog it